Tesla spent a lot of effort in the wireless transmission of power. The power was not free and was generated by conventional means. Google "Wardenclyffe" , it will explain what he was up to.
Thanks Alan
TeslaStuff
Vist my website at TeslaStuff.com for plans, parts and information on Tesla Coils and construction.
Monday, January 28, 2013
Sunday, January 27, 2013
Tesla Generator
There is not a single working model of a “Tesla Generator” that I know of. All the sites I have checked out on the internet are just scams to steal your money. Tesla Coils consume power, they don’t create it. The Tesla Coil parts and packages I sell are for scientific demonstration, teaching and entertainment. Thanks for thinking of me.
Alan
Tuesday, November 23, 2010
Yes, I am still selling my Tesla Coil Plans
The plans for my medium size coil are available at www.teslastuff.com
Thanks Alan
Sunday, September 20, 2009
Tesla Coil Primary Construction
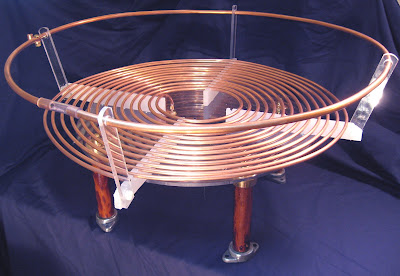
Below is an excerpt from my Tesla Coil Plans available with over 90 pictures (including a
lot more of the primary construction). Available for $12 at my website,
http://www.teslastuff.com/
Place the four 7 inch standoffs at even points on the top pine circle of the base to support the Lexan circle. Find the center of the Lexan circle and use the same procedure we used on the bottom pine circle of the base to mark two lines that bisect the Lexan at 90 degree angles. Use these lines to align the standoffs along the outer edge of the Lexan . Once aligned, mark the points and drill a ¼ inch hole on each one to attach the standoffs. Also drill a ¼ inch hole in the exact center of the circle.
Before we wind the primary, we have to make the support combs(see pictures previous page). You have many different options here. If you Google “Tesla Primary Coil Supports” and hit the images tab, you will see many different versions of ways to support your primary. For our example, I am going to make the combs out of Polypropylene (soft plastic cutting board material). The photos are very detailed and should answer most of your questions on the construction of the combs. Basically, you drill fourteen, ¼ quarter inch holes in a straight line evenly spaced at ¼ inch to 3/8 of an inch apart. The dimensions in our example combs when finished are 1 inch x 9 ½ inches. To allow the copper tubing to be placed in the comb, the top 15% of the ¼ inch holes are cut off using a table, saber or band saw. Try and leave as much of the hole as possible, while still allowing room for the tubing to be pressed in. Some things to keep in mind as you wind the primary. First, don’t unroll the copper tubing. Try and use its original shape to your advantage. You want to keep the amount you bend the tubing to a minimum. The copper tubing tends to become “work hardened” and tough to work with if you bend it to much.
Winding the primary With our four inch secondary, we want the center hole of the primary to be about 5 ½ inches in diameter. Drill a ¼ inch hole in the Lexan about 1 inch from the side of the secondary. This is where the copper tubing will go through the Lexan base so you can make the electrical connection underneath the primary coil. Press the tubing into the combs working your way around until you complete the secondary. I find, adding just a small drop of hot glue works well to hold things in place. Don’t over do it with the glue or you will have a mess on your hands. Take your time. This is a slow process. At the outside edge of the primary coil, when you finish the last turn, you will trim the excess with a tubing cutter and glue the final end in place. Plan on spending about 1 hour after you are done “tweaking” the copper tubing positioning to get a great professional finished look.
Thanks Alan
Sunday, August 16, 2009
The Rotary Spark Gap for a Tesla Coil
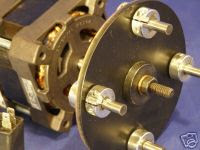
You are looking at an Oriental Motor 1800 rpm synchronous motor, a G-10 fiberglass complete rotor thats under 4 inches! (about 90 mm) with a matching solid copper 18 gauge back plate disk that has been drilled and balanced, a mandrel designed for this rotor and cw & ccw operation, (2) motor run capacitors , (4) each flying tungsten electrodes press fit into the rotor and (2) 1 inch static electrodes with solid copper holders. Some of the pictures you see are examples of the type of Rotary Synchronous Spark Gaps you can build with these, and your added components. When I started into building Tesla Coils, it wasn't long before I wanted a Rotary Gap for my Neon Transformer based coil. In over 100 hours of searching, I found the parts I needed were hard to come by. When I finally did and switched to a rotary spark gap, the increase in performance was incredible!
To get a true synchronous gap I needed a motor that operated as a salient pole type synchronous motor. My only option seemed to be to convert a standard type motor by "grinding or machining the armature" of a standard motor. Not really up for that, I wanted to "buy" a motor that would work "out of the box". I had read about these motors from the Oriental Motor Company called "Reaction Motors" that operate as a "Salient Pole". Hundreds of synchronous spark gaps have been successfully made from them. The suggested surplus model was unavailable and the new replacement in small quantities were $234.00 each. The companies I was directed to (Herbach and others) were all sold out of the surplus version.
After much searching, I found a small lot of these motors that are Brand New Old Stock. I am keeping some for my own use and selling the rest here. I have made over 100 of these and still invest about 2 1/2 hours of time per rotor. I recently added pictures of the latest rotor design, lighter in weight and I have guys using them at 20KV at 75ma in Australia. Also pictured is a new motor run capacitor. I have been looking for a capacitor like this for these motors for over a year. Smaller, the right voltage, value and non-OILCAN look, even has a mounting bracket built in! I had also had so many requests for flying and static tungsten electrodes I decided to include those as well.
Asynchronous motors work fine If you have a "Pole Pig" transformer. If your using a "Neon Sign" transformer they can be really rough on it and may destroy it. The motors I'm selling are rated at 115VAC. With the under 4" rotor and the 4 flying electrodes and 2 static electrodes pictured, (which gives 120 BPS, ideal for most neon sign transformer coils) sync lock is achieved at approximately 90 volts (see picture). You are buying only the items listed above, you will need to supply a base and mount the motor, etc.
The mandrel makes the sync adjustment easy, just align the rotor and re tighten. Its been great talking to all the coilers out there, what a great group of folks from all over the world. These motors will run on 50Hz or 60Hz at 1500 rpm or 1800 rpm for our friends in other countries. I have sold quite a few in the UK and Australia with good feedback from the users. They just use a variac to reduce the voltage. Check out my website, http://www.teslastuff.com
To get a true synchronous gap I needed a motor that operated as a salient pole type synchronous motor. My only option seemed to be to convert a standard type motor by "grinding or machining the armature" of a standard motor. Not really up for that, I wanted to "buy" a motor that would work "out of the box". I had read about these motors from the Oriental Motor Company called "Reaction Motors" that operate as a "Salient Pole". Hundreds of synchronous spark gaps have been successfully made from them. The suggested surplus model was unavailable and the new replacement in small quantities were $234.00 each. The companies I was directed to (Herbach and others) were all sold out of the surplus version.
After much searching, I found a small lot of these motors that are Brand New Old Stock. I am keeping some for my own use and selling the rest here. I have made over 100 of these and still invest about 2 1/2 hours of time per rotor. I recently added pictures of the latest rotor design, lighter in weight and I have guys using them at 20KV at 75ma in Australia. Also pictured is a new motor run capacitor. I have been looking for a capacitor like this for these motors for over a year. Smaller, the right voltage, value and non-OILCAN look, even has a mounting bracket built in! I had also had so many requests for flying and static tungsten electrodes I decided to include those as well.
Asynchronous motors work fine If you have a "Pole Pig" transformer. If your using a "Neon Sign" transformer they can be really rough on it and may destroy it. The motors I'm selling are rated at 115VAC. With the under 4" rotor and the 4 flying electrodes and 2 static electrodes pictured, (which gives 120 BPS, ideal for most neon sign transformer coils) sync lock is achieved at approximately 90 volts (see picture). You are buying only the items listed above, you will need to supply a base and mount the motor, etc.
The mandrel makes the sync adjustment easy, just align the rotor and re tighten. Its been great talking to all the coilers out there, what a great group of folks from all over the world. These motors will run on 50Hz or 60Hz at 1500 rpm or 1800 rpm for our friends in other countries. I have sold quite a few in the UK and Australia with good feedback from the users. They just use a variac to reduce the voltage. Check out my website, http://www.teslastuff.com
Alan
Plans for Building a Great Tesla Coil
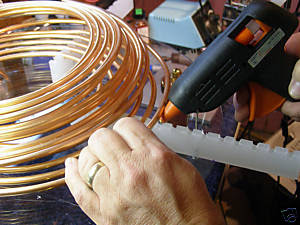
Alan
Subscribe to:
Posts (Atom)